Does Fulfillment Center Location Matter in Ecommerce?
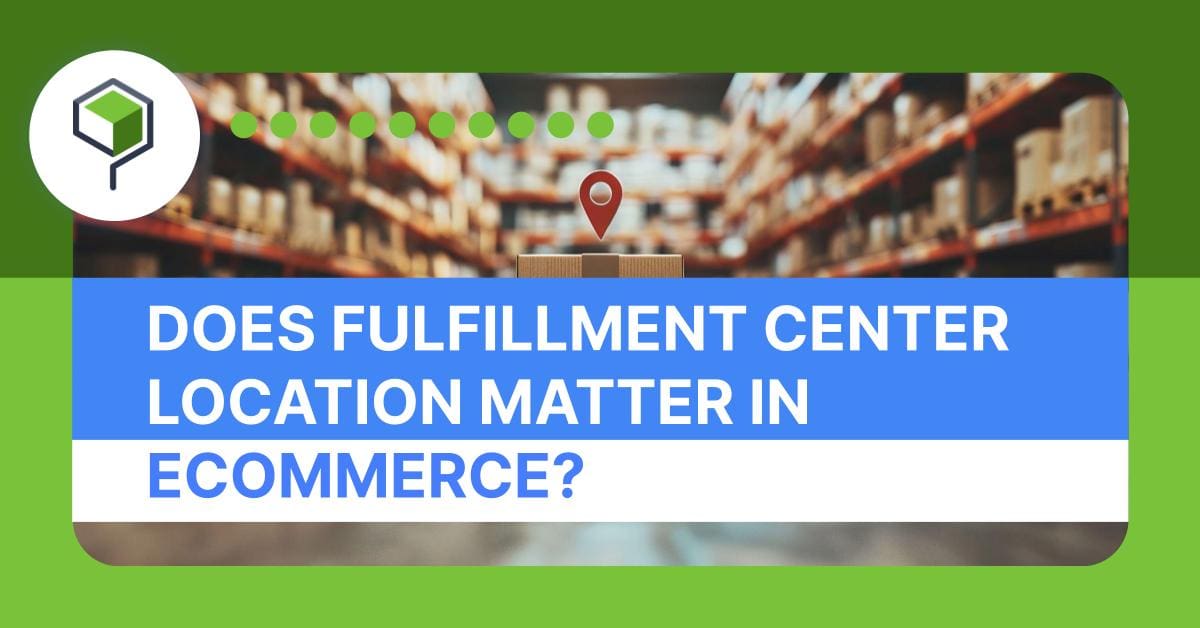
‘What is ecommerce fulfillment?” is one of the most popular questions by ecommerce businesses. But there’s another question that’s just as important; where is ecommerce fulfillment?
No matter how streamlined or technologically advanced your order fulfillment process is, you’ll never reach customers in two days or fewer unless your fulfillment warehouse is located in the right place. No matter whether you have one fulfillment center or multiple warehouses, fulfillment center location is the foundation of your success.
We’re going to dive into the importance of fulfillment center location, what to consider when deciding locations, and why ShippingTree achieves such competitive geographic coverage through just two fulfillment locations.
What is fulfillment center location?
Your fulfillment center location refers to the warehouse space or facility where ecommerce fulfillment is being carried out for your online orders. This is where activities like order processing, inventory storage, picking, and packing are carried out in advance of shipping a completed order to the end customer.
Fulfillment center location plays a massive role in the efficiency and overall success of your ecommerce fulfillment strategy. It impacts everything from fulfillment costs to the average number of shipping zones your orders must cross to reach the customer. Get it right, and your ecommerce business unlocks significant growth opportunities and cost savings. Get fulfillment location wrong, and this costly mistake means more expensive shipping and longer delivery times – and it’s difficult to undo.
Why fulfillment center location is key to success
Being within easy reach of your customers doesn’t just unlock faster delivery speeds – it also determines the shipping costs required to get your order to the doorstep. The fewer shipping zones a parcel needs to cross, the lower the cost of shipping per order becomes. By selecting strategic fulfillment locations, you can ensure that you’ll never be further than a short-haul delivery away.
As customer expectations for rapid delivery continue to increase, your fulfillment center location can be the difference between making good on an estimated delivery date – or missing the delivery window and risking customer churn.
In sum, whether your fulfillment location puts you near (or far) from customers, this either makes shipping cheap (or expensive) and makes delivery fast (or slow). Make sense?
Commonly asked questions about fulfillment centers
Do I need one or multiple fulfillment centers?
While multiple locations for fulfillment can seem like the best way to go, this isn’t a good fit for every ecommerce business. Whether you will benefit from a multi-node fulfillment strategy depends on factors like the size and location of your customer base, order volume, inventory assortment, technology capabilities, and more. One fulfillment center, if it’s in a central location and configured for your precise needs, can still offer value. Check out our blog on multi-node fulfillment to learn more about whether multiple warehouses are the right move for your brand.
Is using multiple fulfillment warehouse locations more expensive?
While using multiple strategically located fulfillment centers does mean higher running costs, this can unlock operational savings in other areas. For example, if your fulfillment centers are located within a 15-mile radius of the majority of your customers, this means much higher coverage of short-haul delivery services, which considerably lowers your shipping costs. Moreover, this also makes fast delivery services like overnight or even same-day delivery more accessible, which creates serious growth opportunities for your business.
Do I need to be close to my fulfillment center?
Not if you’re working with a reliable 3PL partner! While being close to your fulfillment center may feel reassuring and make site visits more convenient, this does mean restricting your choice of fulfillment company. Plus, this could mean choosing a location that’s further away from key consumer hubs, which can push up shipping costs and transit times. Ultimately, if it’s a choice between your fulfillment center location being close to your business or close to your customers, your customers should take precedence.
How to choose fulfillment center locations
Decide what fulfillment services you need
Whether you’re leasing a private facility or partnering with a 3PL, not every fulfillment center location will be outfitted to handle specific services or workflows. For example, if you want to invest in value-added services like kitting or subassembly, you need to make sure that a potential fulfillment center is set up to handle this efficiently. Likewise, certain picking configurations may be advantageous to certain kinds of SKUs but not others, so it’s important to investigate each warehouse space closely to see whether it can serve your needs.
Map out your key consumer hubs
Put simply, your fulfillment centers should be as close as possible to where your customers are, as this lowers transit times and lowers shipping costs. A metro area that has a dense configuration of customers is perfect for a micro-fulfillment center to aggregate shipping and deliver orders quickly. Alternatively, you can look for a fulfillment center that is located close to major highways and transportation routes so that you can access cost-effective ground shipping methods with a quick delivery time.
Decide what delivery speed you want to offer
The faster the shipping method, the more expensive the rate will be. If speeds like same-day delivery are a priority for your business, you will need to select fulfillment center locations that are within a close radius of your customers. Naturally, customer expectations count for a lot in this area; if the majority of your customers are satisfied with standard shipping that takes a few days, you can select fulfillment centers that are further away but less expensive to lease.
What inventory do you need to store
Different types of inventory have different requirements when it comes to shipping and storage. Regardless of whether you are using one or multiple warehouses, your locations must be able to accommodate these characteristics. If you using multiple locations, your inventory assortment in each facility is very important. Some SKUs are going to be more popular in some regions than others, so your assortment needs to reflect this to prevent dead stock and keep inventory moving. For example, hosting snow or cold weather gear in a fulfillment center in Florida makes little strategic sense. But putting these same SKUs in New York will see them move a lot faster at certain times of the year.
Why ShippingTree has fulfillment center locations in Columbus and Los Angeles
At ShippingTree, we’ve put this very advice into action through the fulfillment locations that make up our network. We operate state-of-the-art facilities in Columbus, OH, and throughout the greater Los Angeles area, giving our customers competitive geographic reach across the U.S. mainland.
A central location within easy reach of the Midwest and the East Coast, our Columbus facility is well-placed to ensure coveted two-day delivery speeds on the majority of shipments. For small ecommerce brands with low order volumes, Columbus offers a strategic location for hosting one fulfillment center location, keeping shipping costs down while still allowing for timely delivery.
Los Angeles represents one of the biggest consumer hubs in the country, making it a suitable place to expand your fulfillment network. ShippingTree hosts multiple warehouses throughout the LA area, making next-day and same-day delivery accessible to customers within a 15-mile radius of your inventory.
Whether you’re looking for centralized fulfillment or a multi-node strategy, contact ShippingTree today to find out how you can make your fulfillment center location start working for you.